
Our Quality assurance
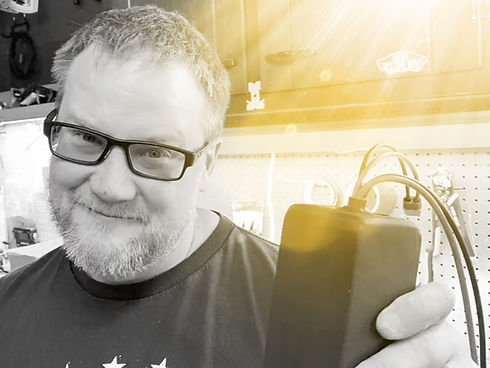
Built in Bethlehem with Pride.
Engineered by Matt Bzura
Serving the eBike Community for 10 Years, Bicycle Motor Works' formula for producing premium eBike Battery Packs is quite simple, yet quickly diminishing in a world of mass production.
Unlike other brands, we set High Quality Standards for every stage of the development, production, materials and distribution process.
Quality Can't Be Rushed
The production process is time consuming, which is why customers are willing to wait 2-3 weeks for their custom-made eBike Battery.
GOLD STANDARD
Worldwide Demand for our High-Current Batteries
-
Pure Copper Bus bars for High Current power
-
Certified Premium Cells by our U.S. Distributor
-
Safest, most reliable BMS in the market
-
Spot welded, sealed and inspected by the engineer
Our Signature process

We, at Bicycle Motor Works, are strong believers in "overbuilding" our packs, for one example we use 0.5mm thick copper busbars spot welded to connect each series. Most packs available today use 0.15mm nickel or in some cases nickel plated steel. Even if a pack is built with quality cells and a high current BMS, the performance can still be underwhelming if series connections are made with thin strips of nickel.
Copper Is 5X More Conductive Than Nickel
Therefore a pack would have to use nickel that is approx. 2.5mm thick to equal the current capacity of our packs. For reference, 2.5mm is thicker than the lead that runs through a #2 pencil.
Current travels through our Packs effortlessly. Because we build our packs with thick copper connectivity, there is little resistance. A pack with the same cells, using thin nickel, will have a lot of resistance in a high current situation.
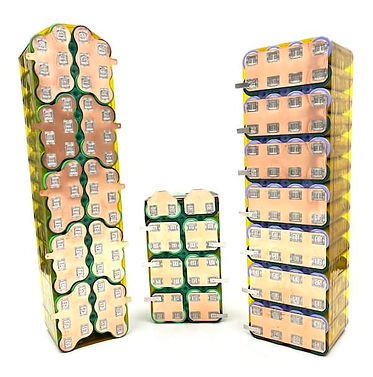

Resistance Equals Heat And Wasted Energy
Heat is the #1 reason for faster cell degradation and a shorter pack life. You will also experience greater voltage sag and less capacity with packs that use higher resistant nickel for series connections.
All Of Our Packs Are Well Protected.
The “shark” cases that we use are from the premier case manufacturer, Reention. The “brick” style cases that we are known for are also VERY durable. After the pack is built, we pad the entire surface then cover it in a hard shell of super-strong Garolite.
Garolite is an industrial grade fiberglass material.
It is created using high-pressure and high temps. Garolite is electrically insulating, puncture resist, fire resistant, and very rigid. We then cover the shell with thick, rubber shrink wrap to add another layer of protection.
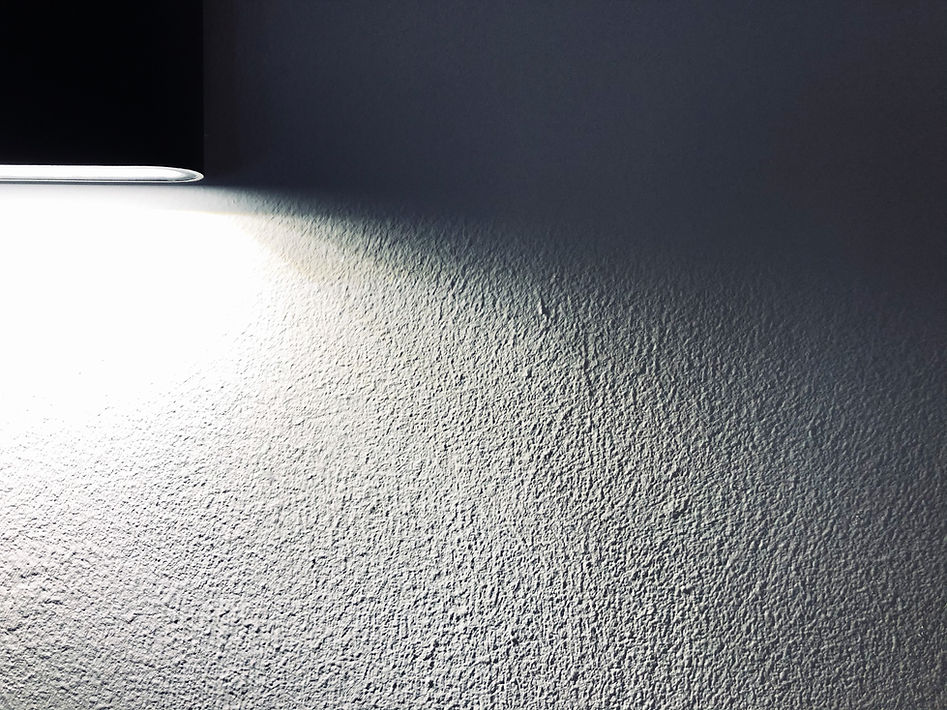
About
CYC MOTOR
In 2018, starting as an university project, Jon Chan (Founder and acting CEO) saw the potential of making high-powered drive systems and what it could mean for the industry as a whole. So, he developed the X1 Pro Gen 1 and got some funding by winning a few fancy awards. With some experience behind him from starting GNG Electric (yup, some of you already know that name), he was off to a good start. Now, he needed a team. A passionate team.
This team is ever-growing and the result? The X1 Pro Gen 2 became one of the first ebike conversion kits equipped with torque sensing. This was great and all, but what else could they do? ISIS torque sensing, our own controllers, what about our own peripherals, smart display, or a system that’s even smaller? They’ve already achieved all of that and it doesn’t stop there, there are more projects happening behind the scenes.
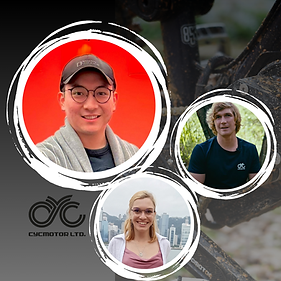